Technical Facilities/Services
- Calibration scope: 10+3 to 10-6 mbar
- Standard followed: ISO 3567:2011 Vacuum gauges – Calibration by direct comparison with reference gauge
- Metrological traceability: International accredited lab
- QMS certification: ISO 9001:2015 from Certification Services Pakistan (CeSP).
- Calibration services for vacuum gauges: Pirani gauge, dial gauge, capacitance diaphragm gauge, spinning rotor gauge, hot cathode gauge, cold cathode gauge, full range gauge etc.
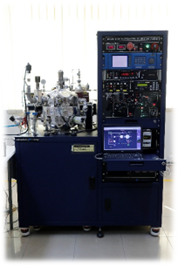
Vacuum Gauge Calibration System VGCS 3000
- Leak testing scope: 10+3 to 10-6 mbar
- Minimum detectable leak rate:
- Vacuum Mode: 5 x 10-12 mbar.l.s-1
- Sniffer Mode: 5 x 10-9 mbar.l.s-1
- Leak testing of sealed components: Helium bombing technique
- Provision of leak testing services: Helium bombing technique
- Vacuum systems, vacuum furnaces, vacuum coating system, welds & joints
- Metalizer plant, cryogenic vessels, vacuum chambers, oil dehydration plant
- Pharmaceutical industry, food industry, packaging industry, automobile industry
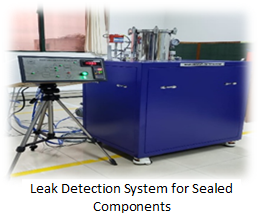
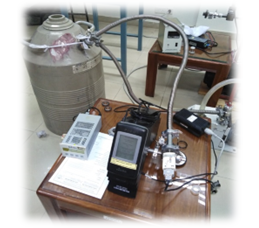
Leak testing / rectification of Vacuum System
- Base pressure: < 1 x 10-8 mbar
- Temperature Range: (23-125) °C
- Standard followed: 5 x 10-9 mbar.l.s-1
- Total mass loss technique (ECSS-Q-ST-70-02C)
- Accumulation technique (ISO/PS 20177: 2018)
- Applications: Qualification testing of materials / components for vacuum and space applications
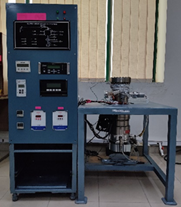
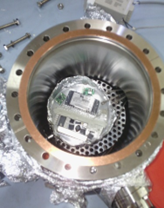
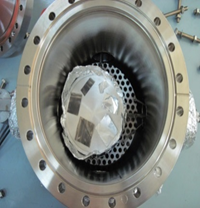
- Vacuum Range: 1x 10-2 mbar
- Temperature Range: upto 300°C (Adjustable)
- Applications: Degassing of epoxy materials/ vacuum components, drying of nanomaterials etc.
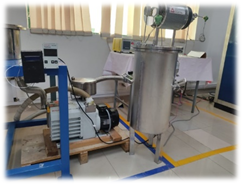
3D Laser Scanner
NINVAST has developed performance evaluation setups using different techniques of the following pumps:
- Rotary Pump
- Roots Pump
- Diffusion Pump
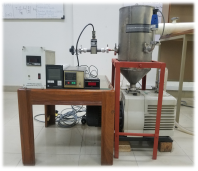
Pumping speed measurement of Rotary vacuum pump
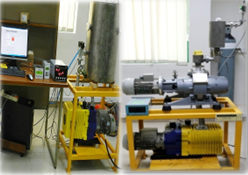
Setup for compression ratio measurement of Rotary / Roots system
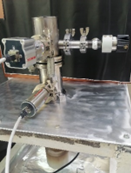
Pumping Speed Measuring Set up for Diffusion Pump
- Scope:
- Pump repair/overhauling facility
- Pump leak testing facility
- Vacuum generation facility up to 10-9 mbar
- Pump performance monitoring via VFD (Variable frequency drive)
- QMS certification: ISO 9001:2015 from Certification Services of Pakistan (CeSP).
- Potential Clients: R&D organizations Universities and industries including; cryogenics, packaging, pharmaceutical etc.
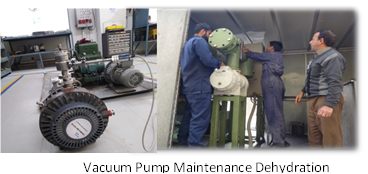
NINVAST delivers following services on user’s request:
- Upgradation of existing vacuum systems
- Vacuum system design & integration
- Equipped with CAD-Modeling, Inventor, Solid Edge
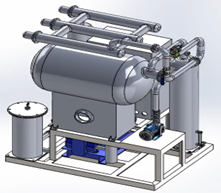
Following facilities are available
- Lathe Machines
- Milling Machine
- Drilling Machine
- Surface Grinding Machine
- Engraving Machine
- Power Hacksaw Machine
- Welding and fabrication facility
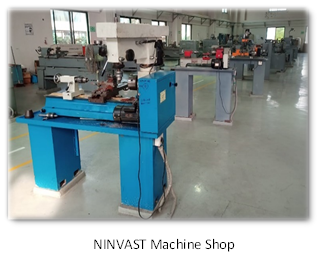
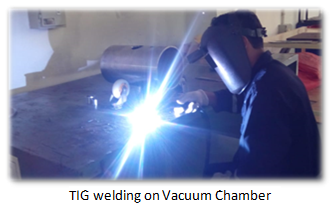
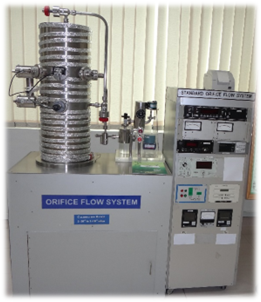
Standard Orifice Flow System
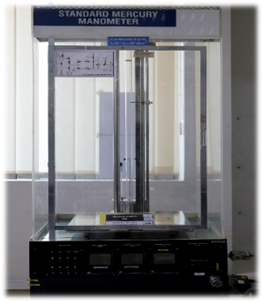
Standard Mercury Manometer
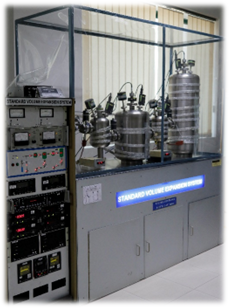
Standard Volume Expansion System
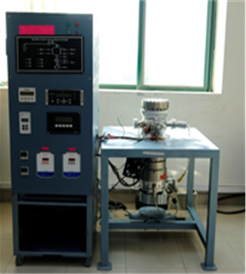
Outgassing Measurement System
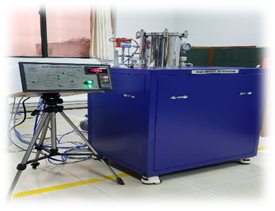
Leak Detection System for Sealed Components
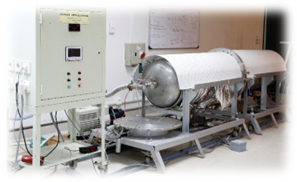
Vacuum Drying / Degassing system
- E-Beam Evaporation System
- Electro-Polished Stainless Steel Chamber (D-shaped Box)
- 4” Diameter View Port on Front Door with Manual Shutter
- Single/Multi Pocket E-beam Sources with Water Cooled Crucible (4cc up to 75cc)
- High Voltage Power Supply (3kW to 15 kW) with X-Y Sweep Controller
- Substrate Size: Maximum 8 inch diameter
- Maximum melting temperature of source material: ̴3000˚C
- Quartz Crystal Thickness Sensor with Deposition Controller (10 A˚ - 100 nm)
- PLC Controlled System
- Applications: ceramic coatings, oxides, compounds, alloys, hard, optical etc.
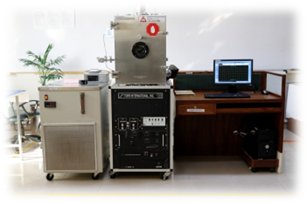
E-Beam Evaporation System
- Thermal Evaporation System
- Sample Size: 450 x 535 mm
- Maximum attainable temperature: 2000°C
- Applications: Optical coatings, metallic coatings, ohmic contacts, thermal reflective coatings, reflective mirrors etc.

Thermal Evaporation System
- PTFE Coating
- Spray technique
- Large area can be coated
- Applications: Anti-corrosion, chemically resistant, self-lubrication, thermal/electrical insulation
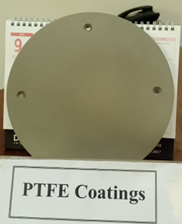
PTFE Coated Sample
- Spin Coater
- RPM: 0 – 5000 (Adjustable)
- Substrate Size: 25mm x 25mm
- Applications: All type of solution based coatings
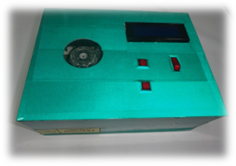
Spin Coating System
- Tube Furnace
- Maximum Temperature: ~1400⁰C with ramp control
- Base Pressure: ~10-2 mbar
- Quartz Tube with glass to metal flanges
- Controlled environment (Argon / Nitrogen, any other gas)
- Applications: vacuum heat treatment, annealing, sintering, drying, calcination etc.
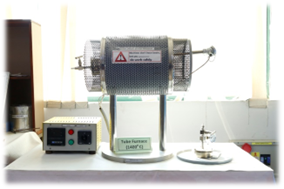
Tube Furnance
- Vacuum Oven
- Maximum Temperature: ~200 ⁰C with ramp control
- Working Pressure: ~10-2 mbar
- Controlled environment:Argon/Nitrogen etc.
- Applications: vacuum heat treatment, annealing, drying, calcination etc.
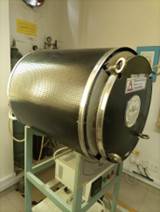
Vaccum Oven
- Autoclave
- Maximum Temperature: ~300 ⁰C
- Maximum Pressure: 3 bar
- Solution capacity: 50-75 ml
- Material: Stainless Steel
- Application:
- Chemical reaction at high pressure without solvent evaporation
- Hydrothermal synthesis
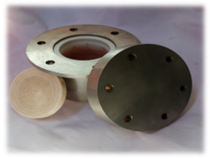
Autoclave